One of the benefits that different types of metal have is the fact that they are relatively ductile. The ductility of metal ensures that they bend before they break, so they can be formed to useful pieces. There are many pieces of forming equipment that can be used to alter the shape of sheet metal, the most common one is the press brake.
Press Brake
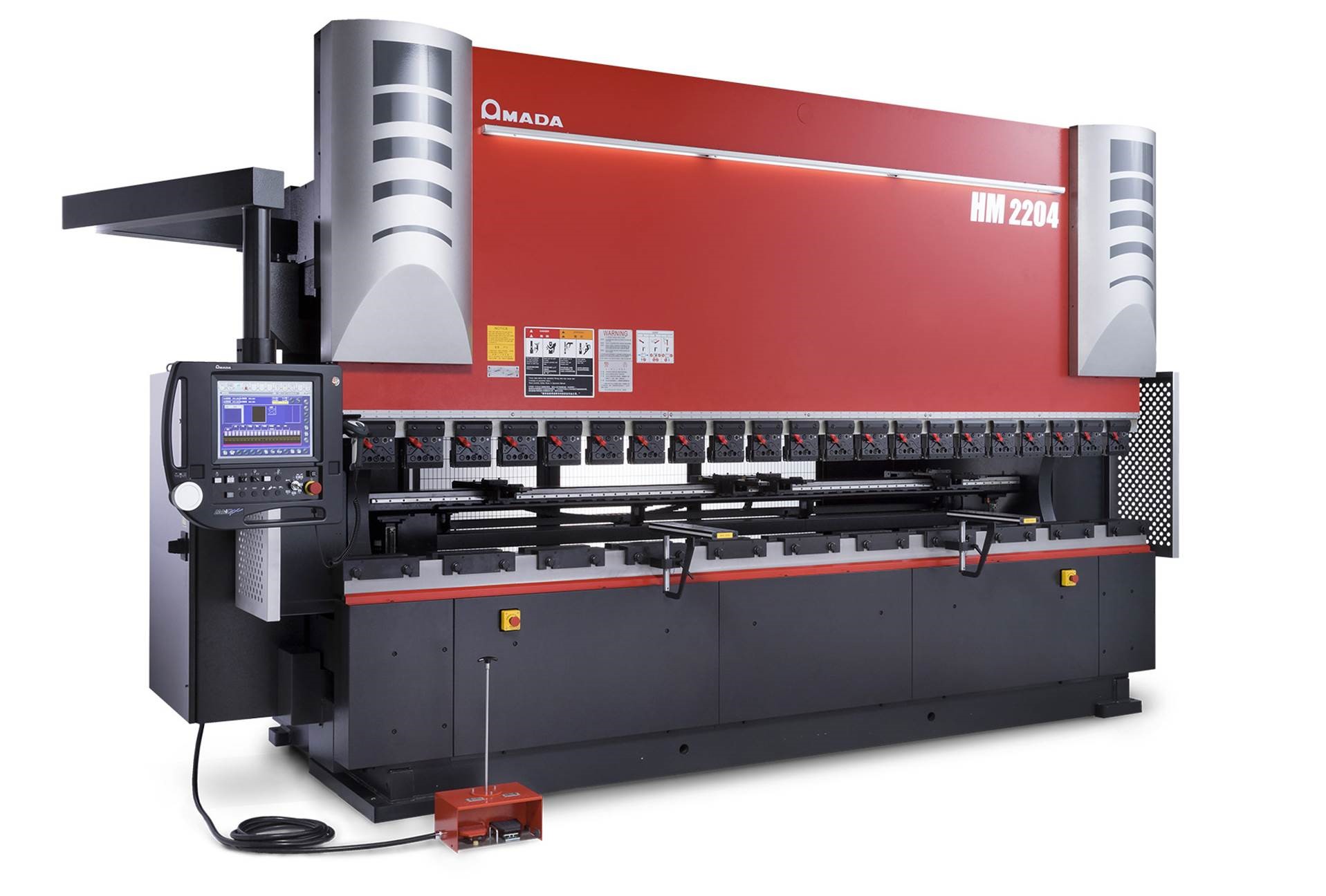
A Press Brake is a forming machine designed for precision metal forming processes. It bends sheet metals to form desired profiles by lowering a punch onto sheet metal that has been positioned on top of a die. The metal can be bent several times by a press brake until the desired form is achieved. A typical press has a width ranging from 4 to 30 feet, and some models can provide up to 4,000 tons of bending force during an operation.
Parts of a Press Brake
The components of a press brake machine can vary depending on what type of drive system it uses, but the basic structure will typically include:
- Bed – Used to rest the workpiece on.
- Ram – Used to push down on the piece(or for it to be pushed up into).
- Dies – Used for the brake’s bed to aid in shaping metal.
- Backgauge – This helps ensure the bend is in the right spot.
- CNC system – Older machines may not have this, though it’s become very common for press brakes made in the last couple of decades.
Types of Press Brakes
Bending sheet metal requires a large amount of force. The methods of force application can either be hydraulic, pneumatic, electric or mechanical. Press brakes vary in the amount of force they can provide, this metric is known as tonnage. Tonnage is a measure of tons of force that a press brake can deliver. Modern press brakes are safer and don’t require as much effort as earlier models. Newer models also have increased speed, quality and efficiency of bending metals. There are three common types of press brakes.
- Manual Press Brakes – Also known as sheet metal brakes. These are the most common type of brakes. Manual brake presses require the user to manually adjust the bending dimensions and angle at each cut. These are best used for the mass production of set bending sizes and angles.
- Hydraulic Press Brakes – Hydraulic press brakes utilize two hydraulic cylinders. This allows for more control and consistent strokes. Often they are classified by their movement, up acting or down acting, each with their own distinct advantages.
- CNC Press Brakes(Computer Numerical Control) – CNC press brakes have the highest precision and customization abilities, utilizing computer software to control accuracy and increase efficiency. A trained operator enters data such as bend angle, plate thickness, width and grade into a controller and the CNC press brake handles the rest.
Uses of Press Brakes
Press brakes are found in every fabrication job shop and many machine shops as well. Their versatility allows them to be used for many more applications other than forming. As one of the many important pieces of equipment in the metal forming industry, the press brake helps deliver custom parts to a wide range of industries.
- Aerospace – No plane can be built without press brakes. Since press brakes allow users to bend and manipulate sheet metal into nearly any desired shape, aerospace professionals use a press brake to angle sheet metal that’s used as protective layering on planes.
- Automotive – Automotive companies can construct several vehicles a day thanks to an assembly system that includes press brakes. Due to the press brake’s ability to easily bend sheet metal, they help increase overall productivity of assembly lines and help build high-quality cars.
- Construction – Metal roofs are incredibly durable, so construction works typically use sheet metal for roofs as they can withstand the elements.
What To Consider
Press brakes, like other CNC equipment, are different in aspect to processing field and technology. It’s important to take in full consideration before you make the decision to purchase one.
- Tonnage – This is referred to as the bending capacity of a press brake. It is the most important consideration while selecting a press brake for your facility. Metals typically have a recommended minimum bend radius that the material can be bent to without damaging it. The metal type is important to understand because of the differing physical properties among metals. Depending on both the thickness and length of the metal sheets, you can end up needing to buy a smaller CNC press brake and cut costs. Here are some of the things to consider when calculating what tonnage you need for the machine:
- Type of Material
- Thickness of material
- Length of Material
- Process Employed
- Die Opening
- Bending Accuracy – If the accuracy requirement of a product you are making needs to be precise, then you would have to choose a press brake with high accuracy and good performance. CNC Press brakes are always equipped with a CNC controller for quick punch installation and clamping.
- Required Tools – While you may already have a set of tools to use, these may not be compatible and might be worn out enough that they may damage your press brake. It’s always best to use the recommended tools to help extend the life of your press brake. For CNC Press Brakes, precision-ground tooling is recommended while conventional tooling is for manual press brakes.
Are you in the market for a high quality used press brake? Contact the experts at Westbrook Engineering and we’ll help you find the right machine for your application. View our entire used metal fabricating machinery inventory here.